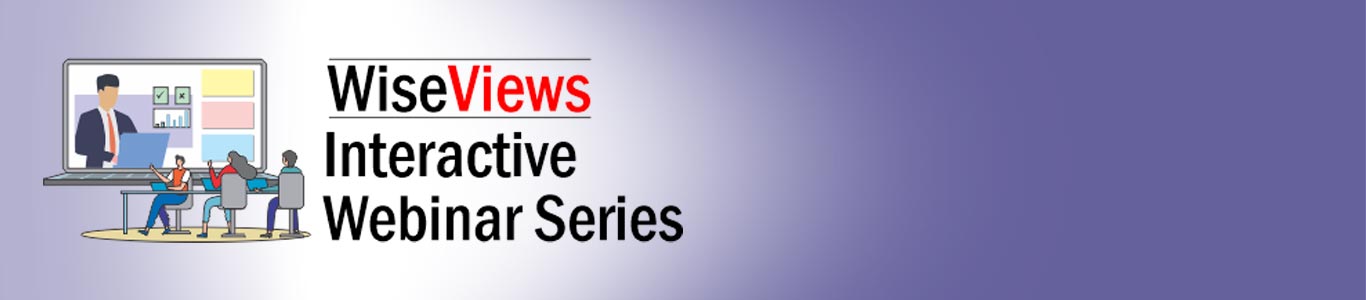
Role of digital in reimagining the supply chain: An evening with Prof Janat Shah
Introduction
On Friday, June 18, we had a very insightful session by Prof Janat Shah, Director, IIM Udaipur on how digital technologies are transforming the supply chain. The session was moderated by our R Prasad and Sudhakar Rao.
Prof Shah was earlier with IIM Bangalore. Under his leadership, IIM Udaipur has progressed by leaps and bounds and become the youngest institution in the country to receive the prestigious AACSB accreditation.
One key point kept coming up again and again in Dr Shah’s session. With the emergence of digital technologies, we have to reimagine the supply chain.
Evolution of supply chains
We have come a long way since the time Henry Ford had stated that customers could have any model that they wanted as long as it was a Model T and any color as long as it was black. Today it is the era of variety and mass customization. Companies attempt to give customers exactly what they want. But with this variety has come uncertainty in demand. Digital technologies hold out exciting possibilities for making the supply chain work more effectively.
The fourth industrial revolution
The first industrial revolution was brought about by the steam engine, the second by electricity and the third was driven by information technology. The fourth industrial revolution driven by digital technologies is also called the second machine age (by Eric Brynjolfsson and Andrew McAfee). In the first machine age, machines substituted physical labor and complemented human beings. In the second machine age, machines are developing cognitive capabilities and can substitute human beings. As the World Economic Forum has put it, the Fourth Industrial Revolution represents entirely new ways in which technology becomes embedded within societies and even our human bodies.
The rise of digital can be seen in the success of Amazon and how it is able to provide a wide variety of goods to customers with very reliable and speedy delivery, sometimes in a matter of hours. GE’s Predix platform and Nike’s customized shoes are other good examples.
The importance of speed
Prof Shah emphasized that we cannot adopt a wait and watch approach with today’s technologies. In the past, it was common to wait till the technology had matured and then implement it quickly. The digital revolution is different in terms of scale, scope and speed. Many digital technologies have been proven and implemented at scale.
Companies like Zara, Amazon and Nestle have already implemented IOT. Kimberly Clark and P&G have improved their demand forecast accuracy using analytics. Siemens in its Hamburg facility produces 12 million PLCs every year, with a wide variety. In the Siemens factory, products talk to machines and the machines talk to each other. Another good example is digital twins. Instead of doing simulations, companies can create a digital replica, test, experiment and then roll out the physical product. Augmented Reality has also evolved.
Mix and match
Success in the world of digital technologies is not about invention. It is about mixing and matching already proven technologies to create a unique value proposition.
Consider Zerodha, founded in 2010 and already India’s largest stock broking company. Using digital technologies, Zerodha has eliminated various frictions which frustrate customers. For example, the KYC process can take weeks in the case of most traditional stock brokers. Zerodha has partnered with an eKYC company to complete this in one day.
The need for reimagination
It is imperative for companies to embrace digital technologies quickly. While doing this, looking at and replacing individual pieces of the supply chain and improving local efficiency will not be enough. Companies will have to reimagine their supply chains, operations and business models. This reimagination will not be easy for most companies as the legacy mindset tends to come in the way.
Consider a tractor manufacturer like Caterpillar. When an equipment breaks down, spares must be made available quickly to get the equipment up and running again. In the earlier paradigm, it would have been about stocking sufficient supplies of spare parts close to customers. But this has become increasingly difficult with greater product variety. Fortunately, it is now possible to use 3 D technology to “print” the spare part close to the customer and make it available quickly. Moreover, a less skilled person at the customer site assisted by a more skilled person sitting at the hub, using AR/VR can easily fit the spare part. Even better, predictive analytics can be used to change the part before any breakdown occurs.
Consider a turbine manufacturer. Instead of selling an asset, it can be converted into a service i.e., enabling customers to generate power and getting paid per unit of power. Digital technologies have the ability to convert assets into services.
Why reimagination is difficult
Prof Paul David’s study
Prof Paul David of Stanford in a landmark study found that when
electrical machines replaced steam engines, productivity did not go up
for 30-40 years. In the case of steam engines, power was transmitted by
shafts and pulleys and all the machines had to be located close to the
power generation equipment. The entire factory was designed around
the steam engine without optimization of the material flows. When
electrical motors first appeared, they were considered a direct
replacement for steam engines. It took time for companies to understand
that there was no need to have a large centrally located electrical motor.
Once the plant was reimagined to optimize material flows, productivity
began to increase.
Additional information (Ref : BBC)
To take advantage of electricity, factory owners had to think in a very different way. Electric motors could do much more. Electricity allowed power to be delivered exactly where and when it was needed.
Small steam engines were inefficient but small electric motors worked fine. So, a factory could contain several smaller motors. As the technology developed, every workbench could have its own machine tool with its own little electric motor.
Power wasn't transmitted through a single, massive spinning drive shaft but through wires. A factory powered by steam needed to be sturdy enough to carry huge steel drive shafts. One powered by electricity could be light and airy.
Steam-powered factories had to be organized around the driveshaft. Electricity allowed factories to be organized on the logic of a production line. Old factories were dark and dense, packed around the shafts. New factories could spread out, allowing natural light and better air ventilation.
In the old factories, the steam engine set the pace. In the new factories, workers could do so. Factories became cleaner, safer and more efficient. Workers had more autonomy and flexibility. So, it was necessary to even change the way they were recruited, trained and paid.
In short, productivity could not improve simply by replacing the steam engine with an electric motor. The entire architecture and the production process had to be changed.
Prof Jayakumar's research
In the 1980s, Prof Jayakumar of Harvard found that after the arrival of flexible manufacturing systems, US companies, compared to their Japanese counterparts were struggling to get the best out of them. The purpose of FMS is high-variety production of many parts at low cost per unit. The average number of parts made by an FMS in the United States was 10; compared to 93 in Japan.
The U.S. companies used FMS in the wrong way-for high-volume production. Thus, the annual volume per part in the United States was 1,727; in Japan, only 258. For every new part introduced into a U.S. system, 22 parts were introduced in Japan.
FMS is more software dependent than traditional production systems. So, the technological literacy of factory workers is critical. In the Japanese companies more than 40% of the work force was made up of college-educated engineers, and all had been trained in the use of CNC machines. In the U.S., only 8% of the workers were engineers, and less than 25% had been trained on CNC machines. Training to upgrade skills was 3 times longer in Japan than in the United States. Compared with U.S. plants, Japanese factories had an average of 2½ times as many CNC machines, 4 times as many engineers, and 4 times as many people trained to use the machines.
In the US, the management treated the FMS as if it were high-volume, standardized production. The management was captive to old-fashioned Taylorism and its principles of scientific management and did not change their mindset.
To summarize, while reimagining the supply chain, companies will have to look at the data flows, information flows and financial flows. Transformation is not easy. It calls for a change in mindset. It also calls for changes while maintaining business continuity. But companies cannot afford to play the waiting game. Otherwise, their lunch will be taken away by someone.
Q&A session
Why supply chains are becoming more important
A supply chain connects the suppliers’ suppliers with the customers’ customers. Some firms operate only in the front end, others only in the back end while very few operate in both ends. Prof Shah argued that the front end is relatively easy to copy. Investment in the backend is needed to generate a sustainable competitive advantage.
The biggest flaw today in SCM is the tendency to be inward looking and lose sight of customer needs. There is not much benefit in trying to become more efficient if it does not help the customer. Thus, if individual customization is the norm, there is little point in emphasizing minimum batch sizes to cut production costs.
Unless the customer is put at the center, the supply chain will not work optimally. While reimagining the supply chain, we should start with the customer, the problem we are trying to solve or the service we are trying to provide and then work backwards. If we look at pieces of the problem, we will work in silos and only increase local efficiencies. We should not break the problem down in the same way we have done in the past. Thus, to keep the equipment running, we should not increase the number of service staff or the spare parts inventory. Instead, we should use sensors to prevent breakdowns and 3 D printing to produce spares close to the customer in case of a breakdown.
On the role of planning and scheduling
In an uncertain environment, planning in advance is difficult. For example, in fashion apparel, with a short fashion cycle, forecasting is not easy at all. In such industries, responsiveness is more important than planning.
Prof Shah recalled his experience with a firm which had a simple manufacturing operation but relatively more complex sourcing and distribution. The company had tried to use a complex ERP system with many functionalities for its manufacturing when there was no need. Technology should be used not for the sake of using it but to solve business problems.
Digitization of operations and marketing
In general, information intensive products are easier to digitize. Zerodha is a good example. In case of physical products, we have to think more creatively about what can be digitized by carefully examining the material, information and financial flows.
Emerging trends
Some things change over time but others do not. This principle also applies to supply chains. Technology changes the tradeoffs while taking decisions. But the fundamentals remain the same. Thus, supply chains should be designed keeping in mind one or both of two considerations: efficiency and responsiveness.
Pooling across geographies, products and time is a time-tested technique of making supply chains more effective. This will not go away. Principles such as postponement of the final configuration and configure to order are as relevant as ever.
But technology has created new possibilities. For example, 3D printing can be used to manufacture goods close to the customer with minimal lead time. For normal standard components used in bulk and where the demand is predictable, 3D does not make sense. But for special, high value components, whose demand is uncertain, 3D can be very useful.
In short, while selecting the technology, we must ask the right questions to see its fit and applicability. We should not be driven by FOMO, the fear of missing out.
The applicability of technology will vary across sectors. Thus, in case of pharmaceuticals, safety and traceability will be of paramount importance. But in the case of skin-based cosmetics solutions, customization may be more important.
While using technology to revamp supply chains, we must remember that the human element will not go away. Take the case of forecasting using AI/ML. Ultimately, these technologies look at past patterns, while making predictions. When the environment changes due to regulation or competition, human inputs are needed to make sure that the models work properly.
The experience of Walmart with RFID in the early 2000s shows that there is no guaranteed success for a new technology. Companies should use new technologies with a spirit of experimentation and keep learning and making changes as they go along.
Understanding the context
What is crucial is that we must understand the context carefully and apply the most appropriate technology. Prof Shah gave the example of ‘oxygen nurse' a term coined in Nandurbar, a tribal district in Maharashtra. The district collector Dr Rajendra Bharud, the brain behind this idea, decided to appoint a nurse for every 50 beds. The nurse had only one task -- to check the oxygen saturation level of each patient. If any patient took off the oxygen mask, the nurse would insist that he wear it. If the patient's condition was improving and the oxygen level was increasing, the nurse would reduce the flow of oxygen and if the patient's oxygen level was decreasing, the nurse would increase the flow from the cylinder. This ensured continuous monitoring of oxygen and the optimum utilisation of the scarce commodity.
Digital and SMEs
Digital is creating a level playing field. Small companies can leverage the cloud to get started without having to make heavy initial investments. These companies can leverage the existing ecosystem to provide a differentiated and valuable service to customers. To succeed, small companies must keep asking: What is it we can offer to customers that the larger companies cannot?
Digital and middlemen
Digital does cause intermediation. But we must remember that the platform itself serves the functions of a middleman. So, the right question to ask is not whether middle men are needed. Those middlemen who can add value will stay and those who cannot, will fade away.
Digital and sustainability
Digital may make things more convenient for consumers. But everything about digital is not environment friendly. For example, shipments at unit level, a trademark feature of ecommerce, is not good from an environmental standpoint. (So many Uber cars on the road are not good either from this standpoint! We would be better off commuting by bus or train.)
Digital and the pandemic
The pandemic is a once in 100 years event. It is not easy to plan for such events. In any case, individual companies will not have the resources or the inclination to do this kind of planning. Such planning is certainly needed but must be done at the level of the society or government.
We should not learn the wrong lessons from the crisis but at the same time we should carry forward the right lessons. We have to do whatever is needed to survive the crisis (History reveals that mankind has moved on after every crisis, including the Spanish flu.) but any investments in long term solutions must be carefully thought through. We must be clear about the kind of responses needed at different levels: firm, industry association and country/world. Positive developments such as online learning are worth taking forward and should become an integral part of life beyond the pandemic.
How IIM Udaipur is reimagining education with digital
IIM Udaipur has invested in a 200-acre Rs 450 crore campus. Looking beyond the pandemic, the plan is to continue with the 2 year and one year MBA programs in face-to-face mode augmented by technology where needed. Executive education will be offered in blended mode.
Prof Shah admitted that he is not sure if this is the right approach. That is the problem for all companies/ institutions with heavy investments already made. If the pandemic had happened in 2011, IIM Udaipur would have approached the problem in a different way as its thinking would not have been weighed down by legacy investments. Legacy investments always limit our imagination.
Prof Shah admitted that for Tier 2 B Schools, the way forward seems to be to leverage MOOCS rather than make heavy investments in developing their own physical infrastructure or content. Prof Shah added that in the years to come, as technology becomes more important, faculty will have to be process rather than content experts. They must be able to leverage high quality content that’s already available and deliver them using state of the art processes.
Realizing that technology will occupy a central place in education, IIM Udaipur has launched a one-year program in Digital Enterprise Management. The learnings from this program will be brought back to the flagship MBA program. It is easier to try out experiments in a smaller program than in the flagship programs.
When it comes to equipping students, Prof Shah emphasized that we must think of the long term, not just the first job from the campus. It is difficult to predict what kind of jobs will exist 5 years from now. So, we should focus on equipping students with fundamental capabilities such as problem solving, critical thinking, design thinking and working in teams.
Some basic knowledge of digital technologies will be essential. Just like we expect executives to know how to use spreadsheets, they will also be expected to be proficient in Big Data. B School students need not become deep technical experts. But they should know how to handle a new technology by asking the right questions and figuring out how to apply it in the right way. That would call for immersion in at least one technology to understand how it works.
On ICFAI’s online MBA program
Prasad explained that unlike IIM Udaipur, the legacy mindset problem did not pose problems for him as he was not incharge of the campus program. But the online program has had to address the typical challenges common among learners these days: poor attention span, lack of self-drive, not doing the required reading and so on. In addition, regulations mandated only one hour of live sessions per week. So how to engage these students for the remaining 9 hours became important.
Prasad and his team drew a distinction between flipped classroom which is applicable to the campus mode of instruction and flipped learning, which is more relevant for an online environment. Given the flexibility and the need to embrace a “guide by the side” attitude rather than a “sage on the stage”, the program had to be tweaked carefully. Weekly interactions with every batch have helped in understanding what is working and what is not. There has been a need to organize content in a way that facilitates organic learning. This is pretty similar to the way people have become aware of various medical concepts during the pandemic through WhatsApp messages and YouTube videos. In short, Prasad and his team have tried to organize learning in a new way and reimagined the various learning activities and processes.
We thank Dr. Vedpuriswar for bringing out the highlights in the form of this note